Distribution Center Design
Doubles Productivity
Overview
MSI Automate implemented a successful distribution center design for snack food manufacturer Old Dutch Foods, doubling the throughput of the previous distribution center operation with just half the labor.
MSI Automate’s distribution center design incorporated warehouse automation technology that included an extensive conveyor system and sortation system with a Sliding Shoe Sorter and MSI Automate’s Warehouse Control System (WCS) as well as a product serialization strategy that enable Old Dutch to track every case of food from the distribution center through in-store delivery.
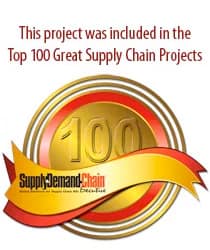
Video Overview
Situation
A leading purveyor of quality snack foods, Old Dutch Foods was founded in St. Paul, Minnesota in 1934. For more than seven decades, the company has been meeting the needs of its U.S. customers with a commitment to high quality, great taste, innovation, and leadership.
Old Dutch Foods also has a strong presence in Canada, from its first manufacturing facility in Manitoba opened in 1954 to 11 distribution centers across Canada today. As part of a strategic initiative to increase penetration of the Atlantic Canadian market, the company acquired competitor Humpty Dumpty in 2000, which added an existing manufacturing and distribution facility in Hartland, New Brunswick to the Old Dutch Foods network.
Opportunity
Though Old Dutch Foods’ strategies have been quite successful in growing the Atlantic Canadian market, it recognized the need to increase efficiency and accuracy if it was to maintain its leadership position, while at the same time upholding its commitment to the existing labor force that had been an important part of the company’s success over the years.
Four key objectives identified by project team:
- Meet efficiency goals by doubling distribution center production with the existing labor force, thereby creating a more streamlined organization.
- Ensure product quality by implementing both lot and serialized control of all SKUs and shipments.
- Eliminate inventory shrinkage through the use of serialized inventory tracking.
- Increase distribution center throughput, processing orders and scheduling trailers at shorter intervals and with faster turnaround times.
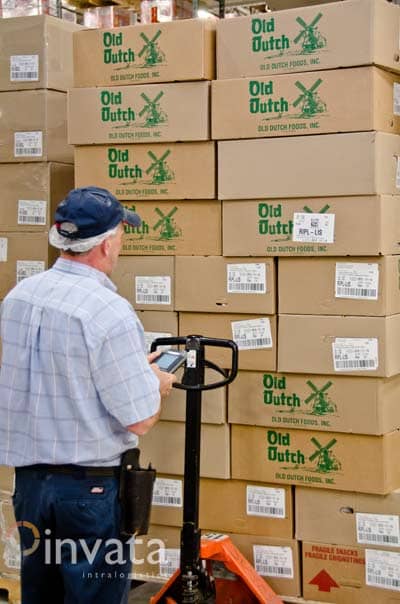
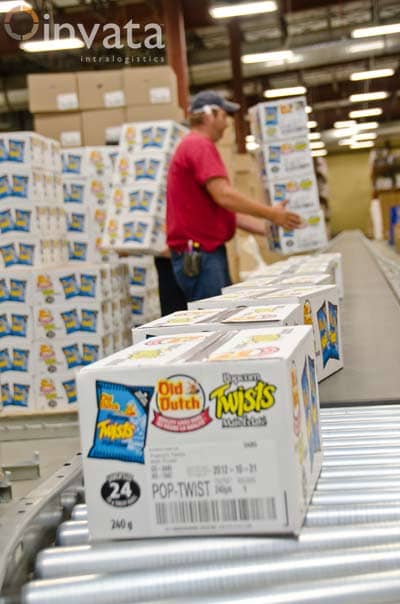
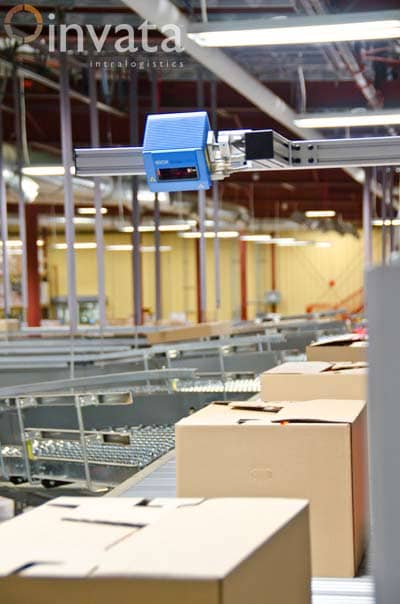
Solution
During the initial design process, Jorn Remmem, Director of Plant Operations and Engineering for Old Dutch Foods, carefully searched for a strategic partner that could provide not only the distribution center mechanization required, but had a track record of success with business process engineering, as well as experience integrating the JD Edwards ERP platform with a Warehouse Control System (WCS) and Warehouse Management System (WMS).
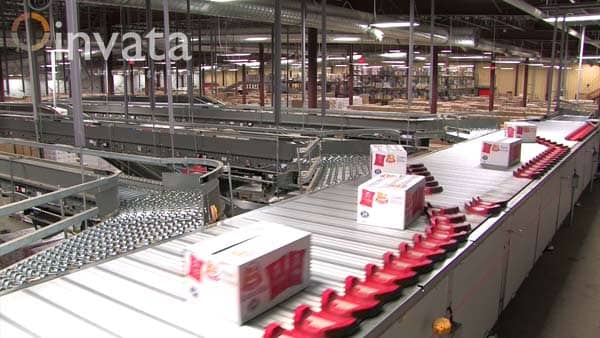
“Probably the most important consideration,” said Jorn, “was that we had a partner we could trust, work closely with, and would be responsive to our needs as we engineered, installed, and integrated the new facility. We found that partner with MSI Automate.”
To achieve its objectives, the MSI Automate team developed a distribution center design that seamlessly receives product from manufacturing and delivers orders directly into waiting trailers.
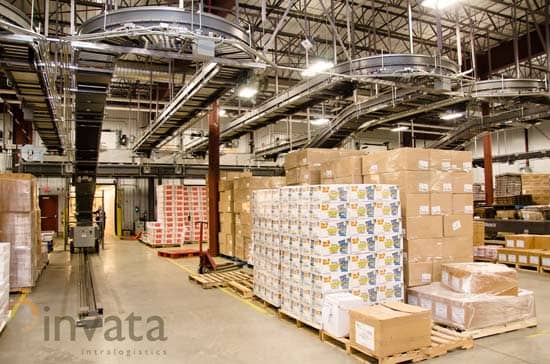
Once the final production operations are complete, cases of manufactured product are moved to the warehouse and staged in a forward pick area. Pallets are staged according to lot, and are serialized for future tracking to ensure first in, first out (FIFO) picking and traceability through the entire manufacturing and distribution process, including delivery to the retail location and, ultimately, the end customer.
The process is initiated when the JD Edwards host computer organizes orders by truckload in reverse stop sequence, and lanes are assigned by the MSI Automate Warehouse Control System. Orders are then batch-picked by generic SKUs and released to RF picking. Cases are promptly loaded onto the shipping conveyor where they are scanned and assigned to specific orders by the WCS, which also assigns the product serial numbers to the order at that time — enabling every case to be tracked to destination. The system enables multiple orders to be processed simultaneously.
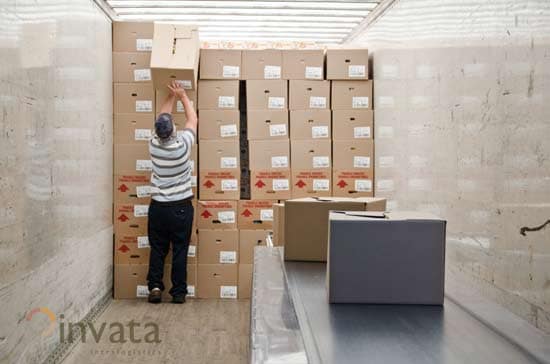
Once cartons have been sorted (via the Sliding Shoe Sorter)by trailer and route, they are confirmed to JD Edwards, and physical shipping documents as well as electronic records are transmitted.
Results
Thanks to MSI Automate’s distribution center design and build out, Old Dutch Foods has achieved its goal of creating a leaner and more streamlined distribution center in the Atlantic regional market; it is now in the process of doubling production to meet growing demand for its products, and is doing so without expanding its staffing. The company has also been successful in achieving its goal of eliminating shrinkage; under the previous system, over 600 cases per month were shipped in error and lost. Today Old Dutch Foods has eliminated shipping errors with the new system that provides complete visibility and traceability from manufacturing to the retailer and beyond.
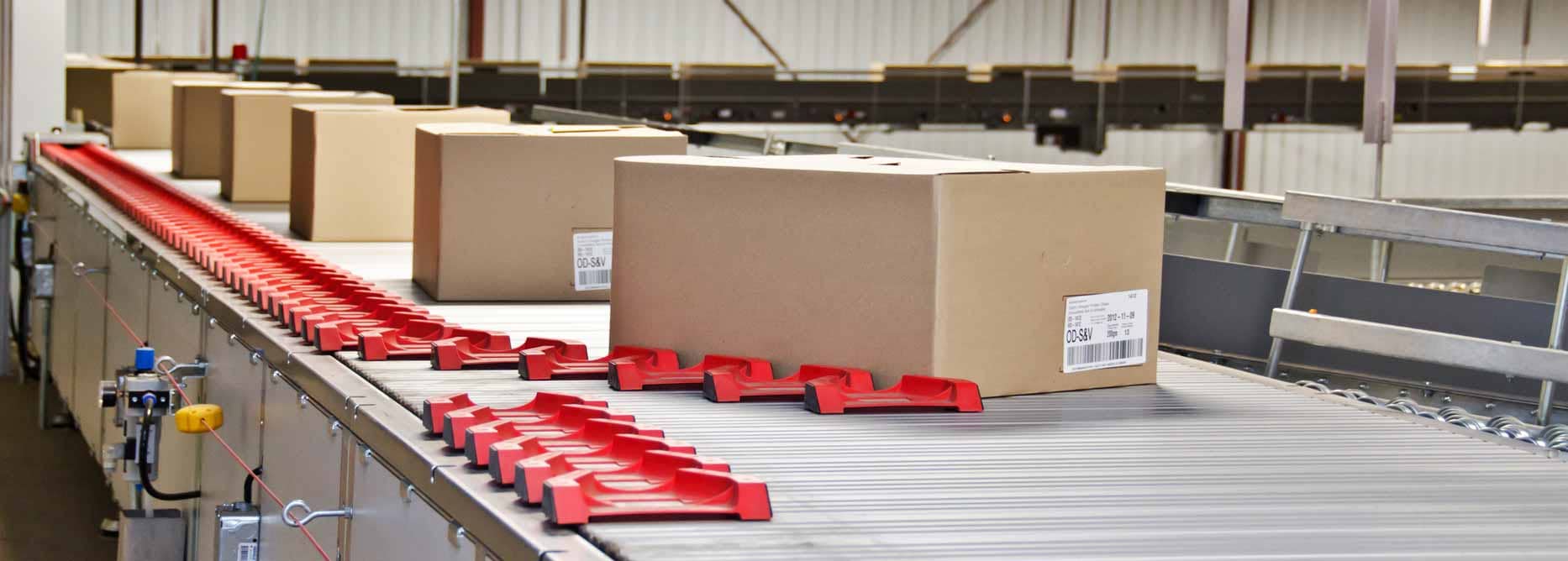
By using new and innovative methods, Old Dutch Foods has successfully completed a major system expansion that is helping to make its supply chain lean and highly responsive, all with lower per unit costs! The system has also demonstrated substantial increases in throughput – meeting their goal of doubling throughput in less time than it previously took to ship half of the volume.