Distribution Center
Best Practices at Work
Overview
Distribution center best practices provided the foundation for MSI Automate’ design and build out of new distribution center for a blood management company.
A global leader in blood management solutions, this client offers solutions for each facet of the blood supply chain, including blood and plasma component collection, the surgical suite, and hospital transfusion services.
Their products include a comprehensive portfolio of blood collection and management devices and consumable blood products, information management, and consulting services.
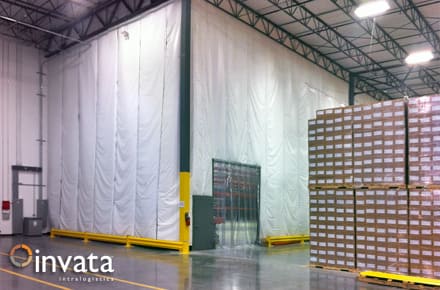
MSI Automate’s distribution center best practices included a warehouse within the warehouse to create a temperature controlled area for temperature sensitive phamaceutical products.
Located in Tennessee, the 145,000 square foot distribution center facility was designed to receive, process, and ship blood management devices and consumables for national distribution to hospitals, surgical suites, and blood collection organizations. The distribution operation, while simple in nature, relies upon distribution center best practices to ensure and maintain the quality of the product line from receiving through shipment.
The facility has been set up to handle processing of everything from an individual carton of blood bags to an entire pallet of consumable products and machinery.
Situation
Prior to the creation of this facility, this MSI Automate client utilized several distribution facilities located in areas either adjacent to manufacturing plants or in 3PL’s around the country. Having concluded it would be advantageous to bring their distribution operation under one roof, the company decided to move their operations to a larger facility. The questions were how large a facility would the new operation require, and what kind of systems would best satisfy the needs of the combined operations?
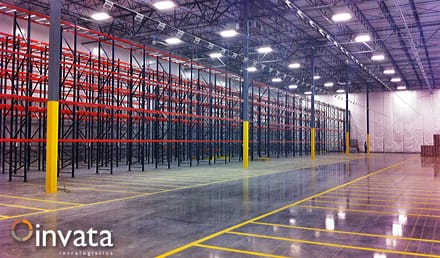
Inside the near 28,000 sq. ft. temperature controlled area is both pallet racking and deep lane storage.
Processes had to be designed for receiving, put away, replenishment, order selection, and outbound shipping. In addition, whatever distribution center best practices were put in place in the facility had to be compatible with the capabilities of the ERP/WMS system already in use within the company and be compliant with the lot control/serialization methodology utilized in the company’s storage and order selection strategies.
The company also wanted to minimize labor requirements wherever possible in the distribution center operation.
A key requirement of the new system was to find ways to store goods in an efficient and highly accessible manner. That meant dealing with numerous high volume items that would be received in large serialization lots and dealing with lower volume items, such as machines, which were individually serialized. All products would need to be accessible at any time. Other requirements included products that could not be stacked as well as products that would require a temperature-controlled environment.
Opportunity
Before a determination could be made on how big the new facility needed to be, a consensus had to reached on which distribution center best practices would be followed, including the kind of storage systems, inventory handling methods, climate control measures, and security measures that would be used in the facility.
Once consensus was reached, MSI Automate was given data on existing sales and inventory levels as well as a list of the company’ s objectives for the new operation. These objectives included:
- Minimizing reliance on labor where cost justifiable.
- Providing temperature-controlled storage for temperature sensitive inventory items.
- Maintaining first-expiration-first-out (FEFO) processing for all lot controlled items.
- Designing the facility to accommodate inventory presently at outlying facilities.
The data was validated, and MSI Automate began the analytics process that would be used to developed a prototype design of the new facility. Once the analysis was complete, the results served as the criteria for the MSI Automate distribution center design. Once the design was agreed upon, the build-out began.
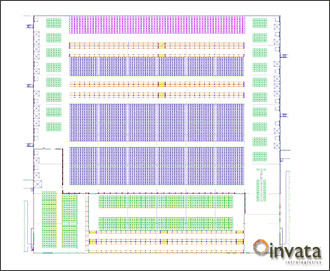
The distribution center design allow products to be stored based on physical characteristics, storage temperature requirements, lot release date, and overall inventory level.
Distribution Center Best Practices
Receiving
Truck trailer loads of blood products are received at the distribution center from sterilizers and distribution and manufacturing facilities throughout North America. As the products are received, they are palletized and temporarily stored in a staging area while awaiting put away.
Put away is determined by a number of factors, including the product’s physical characteristics, storage temperature requirements, lot release date, and overall inventory level. Depending upon a product’s storage requirements, the product may end up in an ambient temperature storage area, a temperature-controlled area, or a quarantine area, and may be stored in a variety of configurations from bulk storage to rack storage.
Lot and QC Hold
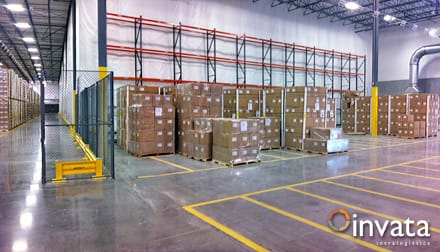
Distribution center best practices prevent mixing of products approved for release with products still pending test results, so a quarantine area was set up within the warehouse to accommodate non-release status goods.
Large lots of blood products are sometimes received in what is known as a non-released status, which means the test results for that lot were still pending while the product was in shipment. Since distribution center best practices prevent that product from being mixed with product that has been released for shipment, a fenced, quarantine area was provided within the warehouse for the staging of these lots, until tests results confirm their release status.
The quarantine area is large enough to accommodate multiple trailer loads of product, should the need arise.
Curtain Wall for Temperature Controlled Storage
This company has a number of temperature sensitive pharmaceutical products that require a temperature-controlled area to protect them from exposure to the Tennessee heat.
Since the distribution facility is housed in a leased space, MSI Automate recommended the installation of insulated curtain walls to create a temperature-controlled warehouse within the warehouse.
In doing so, MSI Automate enabled its client to avoid costly, time consuming construction of new walls that could not to be relocated, were business needs to change.

Vinyl curtain walls create a 28,000 sq. ft. temperature controlled area within the warehouse, providing R6 insulation while saving on construction costs.
Ambient Temperature Storage
Since many of this company’s products come to the facility in trailer quantities from manufacturers, distributors, and sterilizers, MSI Automate was able to employ a unique storage strategy: Products that are received in large lots, are deep lane stored on the floor on pallets, stacked two-high. This greatly reduces the number of aisles needed in the warehouse and saves a great deal of floor space.
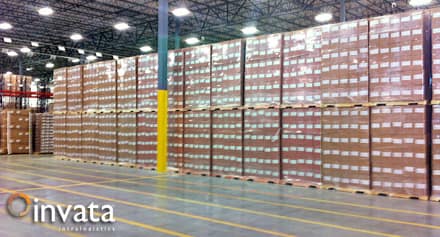
Ambient temperature storage area includes deep lane storage of product lots, providing maximum use of available storage.
Products are then accessed from the front of the aisle for order picking purposes as either complete pallets or individual cases to be consolidated into mixed pallet shipments.
Lanes accommodate picking via either counter-balanced forklifts or walkie/rider pallet trucks. When a lane is empty, another lot can be stored in that location.
Results of Implementation
The distribution center best practices that MSI Automate designed into this client’s 145,000 square foot warehouse has enabled the company to accommodate its complete portfolio of devices and consumables under one roof, while maintaining strict quality control standards, adhering to FEFO processing standards, and complying with a lot control/serialization methodology used in order selection. It has enabled products to be handled according to physical characteristics, storage temperature requirements, lot release date, and overall inventory level, and minimize the labor required to fulfill orders.
The distribution center facility was completed and delivered on schedule, and the success of MSI Automate’s distribution center best practices has allowed the company to close its legacy distribution facilities.
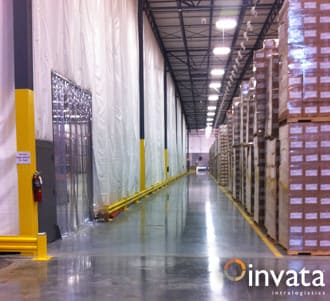
Distribution center best practices combine ambient temperature storage with temperature control storage to accommodate strict quality control standards.
To learn more about MSI Automate’s distribution center best practices, including our expertise in warehouse automation and the warehouse execution software that controls conveyor systems, sortation conveyors, automated storage and retrieval systems, and a wide variety of order fulfillment systems, contact us, and we’ll be happy to share more about our rich history of employing material handling technology to enhance operational productivity.