Fulfillment Center Design for
Luxury Retail Ecommerce
Overview
This fulfillment center design project for a luxury retailer included a packing and shipping system that seamlessly integrated with a Kiva receiving, storage, and picking system. The MSI Automate designed and built ecommerce warehouse automation project incorporated MSI Automate’s Warehouse Execution Software, an automated conveyor system and sortation system nearly a mile in length, in-motion label application, in-motion weighing, dimensioning, bar code ID scanning system, and an interface with Agile Pack and Agile Elite software from the Agile Network. Thanks to this MSI Automate fulfillment center design, our client now has its first fully dedicated ecommerce fulfillment center through which it can now can now keep pace with marketplace demands.
Video Overview
Situation
From its inception in the 1920’s this major retailer quickly established itself as a world renowned leader in luxury goods who had a dedication to delivering an extraordinary product selection and exceptional service to its customers. Since then the company has been true to its heritage, and as a result has grown considerably.
Today the company is an omni-channel, luxury retailer offering its customers distinctive fashion apparel, shoes, accessories, jewelry, cosmetics and gifts. Going to market through several major brands, the company maintains relationships with leading designers including Armani, de la Renta, Dolce and Gabbana, Chanel, Gucci, Prada, Louis Vuitton, St. John, Hugo Boss, Ralph Lauren, and many others. They have introduced online flash sale events and pioneered a number of eCommerce initiatives including user reviews, improved search tools and product videos to improve the online shopping experience.
Opportunity
With over 100 stores nationwide, almost 8 million square feet of bricks and mortar retail space, and initiatives to expand internationally, the company maintains bi-coastal distribution centers to support its network of retail stores, thereby reducing shipping and transportation costs, as well as optimizing and reducing the time to deliver initial inventory and replenishment transactions to support the point of sale.
The company purchases significantly more inventory to meet consumer demand, which also peaks in the months of November and December. These demands are met with substantial increases in warehouse staffing, and the need for additional automation capacity to ensure that the company meets its primary mission – an unwavering commitment to the rich heritage of innovation, quality, integrity and customer service, a common thread across the company and its three major brands.
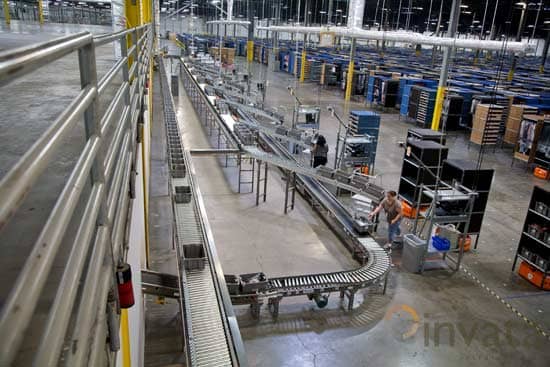
From the initial rollout of their ecommerce initiative, the web channel has proven to drive a significant increase in cross channel business and revenue – as well as an increase in costs. The decision was made to invest in a dedicated ecommerce distribution center that would be located near a major parcel carrier distribution hub, thereby decreasing the time to deliver customer orders, and increasing service levels.
Among the primary goals were the following:
- Reduce labor costs; especially to handle single line orders, and efficiently scale for seasonal peaks
- Provide an ergonomic and efficient method for balancing picking and packing operations
- Reduce shipping costs and time from order to customer receipt
- Design redundant systems in key areas of the facility
- Design and implement the system with minimum IT support
- Easily assign/reassign “logical” carton shipping destinations
- Improve customer service
Solution
One of the most important elements of the project was to build a team that could work together to implement an automated solution for the business. This solution would encompass a complete and seamless order fulfillment center operation, while achieving the business goals and objectives for the new facility; to quickly and efficiently manage the flow of goods and information, from receiving through packaging and shipment, with complete visibility and control, and at the lowest possible cost.
All goods in the storage and retrieval area are inventoried by lot number and handled in a FEFO manner for tracking throughout the distribution process.
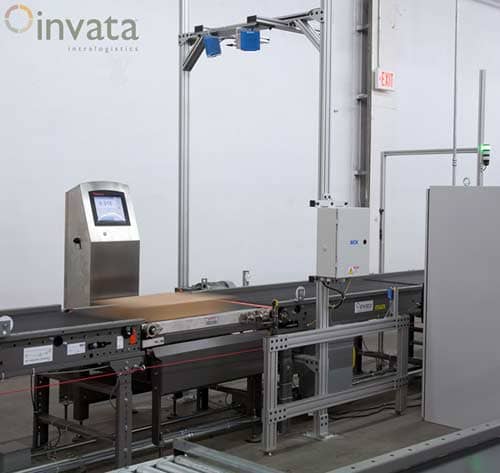
To achieve its objectives, the project team developed a solution that included MSI Automate’s Warehouse Control System (WCS), an automated conveyor and sortation network that would be integrated with a Kiva robot system. It included an automated print/apply system, packaging management software and Transportation Management Software (TMS) applications; Agile Pack and Agile Elite. The overall solution manages receipts, putaway of merchandise in highly flexible and reconfigurable carriers, manages order picking through a network of picking stations, to packing and shipping – all with rendundancy designed into key areas of the facility.
The facility itself utilizes Electronic Data Interchange (EDI) extensively between its suppliers and the company, making inbound operations simpler and faster. Appropriate carrier configurations and available locations are delivered to the receiving operators where items and their locations are scanned to ensure system wide accuracy.
Ecommerce orders are immediately routed to the new facility where they are released to optimized picking zones for single line orders, or multi-line orders. Dynamic order sequencing is utilized to ensure that picking workstations are constantly replenished with new work. MSI Automate warehouse software can manage larger SKUs that can’t be handled by the primary Kiva storage system, while it also delivers a constant supply of order totes to the primary picking workstations – helping maintain an efficient balance between order picking and packing.
To ensure simplicity, intelligent order and shipping labels are used extensively. The MSI Automate software routings can be changed at a moment’s notice to reflect a changing mix of packing needs and order profiles, including value added services such as gift wrapping and gift cards. A seamless interface with Agile packing software ensures that orders are packed accurately and precisely to meet customer needs.
Once complete, up to 3,600 orders per hour can be routed by the MSI Automate WES to the shipping sorter and carrier. To reduce shipping costs, box dimensions are tracked, accurate weight is added via a real time, in-motion scale, and a bank of print/apply machines affix final shipping labels accurately and automatically to each package just before shipment, guaranteeing the best freight rate available, prior to being sorted to their destination shipping lines.
"The new system met its goal of managing the flow of goods and information, from receiving through packaging and shipment, with complete visibility and control, and in a more economical fashion."VP Operations, eCommerce Retailer
Results
In a highly competitive market, the company is now able to ship customer orders within two hours of receipt, with important added benefits; the quality and accuracy of the customer order is nearing 100%. The company also succeeded in commissioning their first, dedicated ecommerce facility, on time and on-budget, with minimal IT support. Not only are space and resources managed more efficiently in the new facility but the system design added important capabilities in the areas of redundancy, flexible pack lane assignments, balanced pack station activity and allowing easily reconfigurable ship lane routing. Shipping costs are also at an all-time low, with a new system that helps to reduce excess shipping charges that can be as high as 30% of a retailer’s freight bill.
And lastly, the company is in a better position than ever to deliver on its customer promise; an unwavering commitment to the rich heritage of innovation, quality, integrity and customer service.