Batch Picking Slashes
Order Filling Labor
Overview
The MSI Automate team was tasked with automating and implementing a batch picking operation built to accommodate the requirements of an omni-channel distribution strategy for one of the largest Caterpillar dealers in the country, Cleveland Brothers CAT in Bellefonte, PA.
The resulting batch picking system services walk-in business, will call orders, route delivery, and branch distribution. Utilizing MSI Automate’s FastTrak Warehouse Software and a tightly integrated material handling system, the system addresses all aspects of the receiving and put-away as well as batch picking, consolidation, packing, staging, shipping, and loading.
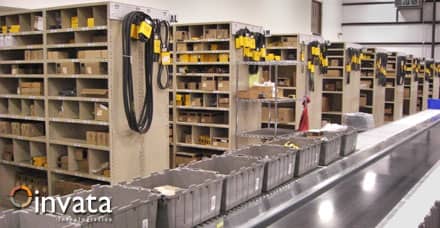
Batch picking is done to totes, which orbit eight picking zones on a conveyor that runs throughout the facility.
As a result, customer service has dramatically improved while the labor needed to operate the facility has been greatly reduced. The new facility has proven itself during times of peak demand and successfully met all expectations.
Situation
Cleveland Brothers had a number of improvements they hoped to make to their distribution system with the implementation of a new batch picking operation.
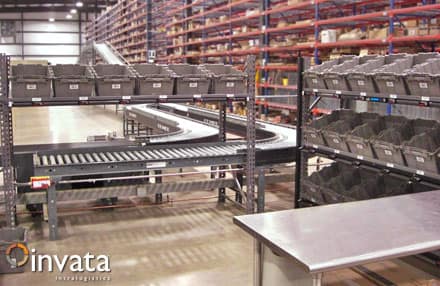
A receiving put wall is used to sort incoming goods and consolidate them for put away via a zone routing system.
They wanted to find a way to ensure that no one waited at the walk-in counter and that all will call orders were ready as promised. They wanted to ensure that route deliveries were dispatched on time and loaded in trucks in reverse run sequence. And they wanted to keep their branch locations fully stocked through accurate and timely stock deliveries that segregated in-branch pickup orders from the balance of the shipment in a way that would position them for expedited handling upon arrival at the branch.
They also wanted to cut down on labor costs associated with receiving and put away, continue to utilize the TecSys WMS in use at theirs and multiple CAT dealer locations, and automate their operation in a manner that would bring their entire system under a single support umbrella with a single interface to the TecSys WMS.
Previous implementations at other CAT dealers had utilized disparate, routing, sortation, and PTL systems and databases, so the Cleveland Brothers wanted another approach.
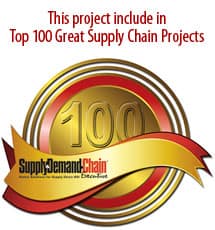
Opportunity
Working with Boston Industrial Consulting, Cleveland Bothers had already chosen a location for the new distribution center as well as a concept of the new operation. The challenges for the MSI Automate Team were to find a way to implement the omni-channel distribution model Cleveland Brothers needed, while integrating the required systems with their existing WMS.
To make the system a success, there were several other challenges the team would need to address as well:
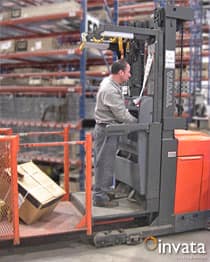
Large item picking via fork truck.
- Minimize labor in receiving by implementing a scanning and sorting process for all incoming goods.
- Reduce put-away labor by curtailing the number of trips through storage aisles.
- Associate orders to totes and route those totes through the picking areas. Batch pick to totes to reduce walking during the picking process.
- Sort picked items from the totes, and consolidate those items with other items that were picked off line (large parts, requiring carts or forklifts for movement).
- Sort outbound parcels to the appropriate carrier lines.
- Seamlessly integrate all system solutions with the TecSys WMS.
Warehouse Solution Overview
The team at MSI Automate successfully implemented the following into the Cleveland Brothers distribution center:
- Consolidation and Put-to-Light systems for receiving.
- A zone routing system for use in picking and put-away.
- A consolidation/sorting system for the batch picking operation.
- A sortation system for shipping.
Utilizing MSI Automate’s Fasttrak Warehouse Software , the MSI Automate team “filled the gaps” in functionality between the TecSys WMS and the new material handling systems, seamlessly integrating the entire operation into a single, common database.
Receiving Solution
The receiving operation in the CB CAT distribution center works in the following manner:
A Put Wall is used in receiving to sort and consolidate incoming parts for put away in the CAT facility. To set up the Put Wall for receiving, totes are associated with a slot location within the wall via a scan of each tote’s serialized bar code ID (PID). Once totes are in place, light displays instruct operators where (in which totes) to place incoming parts.
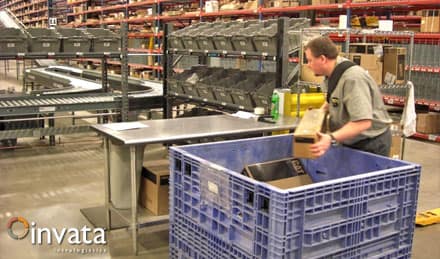
Operator unloads shipping container to receiving desk for processing.
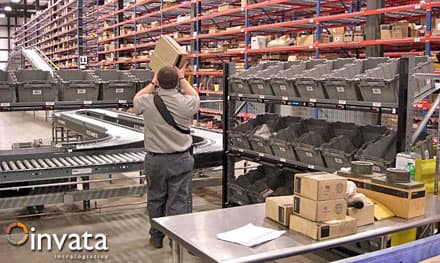
Incoming parts are received into a put wall to enable consoldation of goods for easier put away.
Parts are received from the CAT factories as well as other suppliers in either mixed pallets or in large, mixed container boxes (gaylords). As items are removed from pallets and containers, they are scanned with a radio frequency (RF) device, which triggers a put light, signaling to the operator the corresponding tote in which to place the part. The operate places the part in the tote and extinguishes the light by pressing a button, completing the transaction.
Once a tote is full, the operator closes the tote via the put display function button. The tote is then removed from the receiving station for transportation to a zone within the warehouse for put-away. This receiving/sortation process confirms the receipt of all items arriving in the warehouse, while consolidating items with similar storage locations to reduce walking and searching during the put-away process.
Batch Picking Solution
In order to maximize efficiencies during the order picking (and put-away) process, a zone routing system was established that divides the warehouse into eight sectors. Pickers are assigned to zones as are the totes that are used to transport picked items to order consolidation and sortation. A conveyor system runs throughout the warehouse transporting totes between picking zones and processing functions.
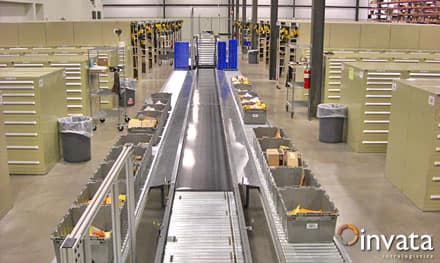
Items are batch picked to totes, which are transported between picking zones via conveyor in this batch picking system.
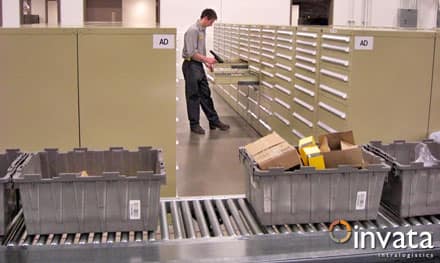
Picking is done in zones. Operators are directed via RF devices through the most efficient order fulfillment path.
Picking is generally done to individual totes along the conveyor or to groups of totes on carts, depending upon the location of the parts to be picked. Orders are assigned to totes based upon their location in the warehouse and the availability of resources to be used to process the orders at any given moment (i.e. pickers, put wall availability, sortation, etc.).
The allocation of available resources is a critical component of this system as continuous real time processing is needed to optimize order fulfillment. FastTrak’s ability to continuously analyze resource availability and direct resource allocation on the fly enables this system to continuously operate at peak efficiency.
Both the carts and totes are routed through the system in the most efficient path possible to optimize the picking process. If a zone is not available for picking at any given moment, the totes associated with the items to be picked in that zone can orbit on the conveyor until that zone or another zone is available for picking.
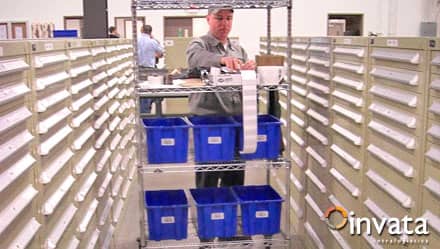
Picking is also done to carts in the batch picking system.

Picked item is scanned via RF device, which registers item against its order and the totes into which it is batch picked.
Empty totes for batch picking can be started in any zone in the system. Pickers are directed through the system via RF devices to the next closest pick location. When a picker arrives at a location, the selected item is scanned to confirm it is the proper part to be picked and is then placed into the assigned tote. The picker then scans the tote, which acts to confirm the transaction was executed properly.
When picking is finished, the completed tote or totes are routed to a consolidation/ sortation “put wall,” where the batch picked items in the tote(s) are sorted/consolidated into individual orders. The put wall is comprised of a grid of divided shelves with light displays that direct put wall operators through their job.
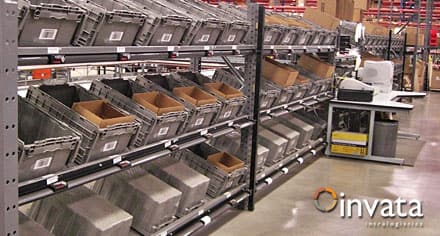
Put wall where batch picked items are sorted / consolidated by orders.
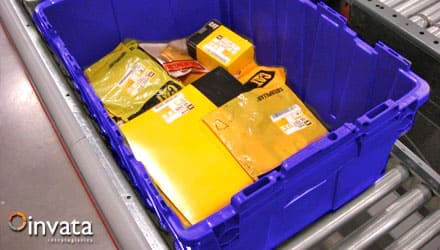
Batch picked tote on route to put wall.
When a batch picked tote arrives, items are removed individually and the item bar code for each is scanned. FastTrak then references the item against an order and triggers the appropriate put-to-light module, indicating where the item should be placed. The operator places the item on the appropriate shelf, or in a tote on the shelf, and then extinguishes the light via the function button on the display.
This continues until the tote of batch picked items is empty or an entire order has been consolidated.
When an order is complete the operator is directed via the display (flashing) to remove the items and pack them for shipment. To do this, the operator moves the goods to a pack bench and extinguishes the light via the function button on the display. Once packing is complete, the order is either staged on carts for customer waiting or will call, put back on the conveyor for sorting to various shipment methods, or sorted to waiting bulk (gaylord) containers for store orders consolidation.
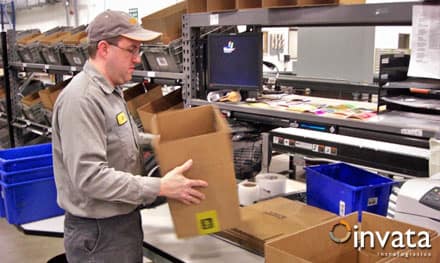
Packing station where picked orders are packed for shipment.
Store consolidation orders are done via put-to-light as well. Orders arriving from the small parts pick area are scanned and light modules direct the operators to place the packages into the waiting bulk containers. Other larger parts arrive via forklift, order picker, and cart. They are scanned in a similar manner to items arriving at the receiving put station and the order is consolidated.
Results of Batch Picking Implementation
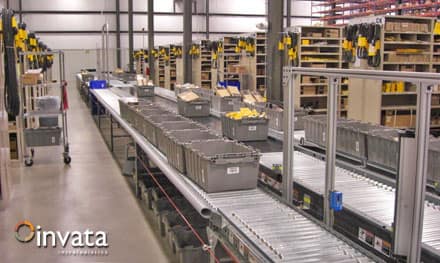
The batch picking system slashes labor requirements associated with both receiving and order fulfillment by optimizing both resources and productivty.
The batch picking solution MSI Automate integrated for Cleveland Brothers CAT, enables them to provide a high level of service to their walk in and will call customers, while optimizing warehouse productivity. The system is able to meet the requirements of same and next day service to their route delivery clients and remote branch operations. And it requires comparatively few employees to run the entire system.
The batch picking integration also leveraged the capabilities of FastTrak Warehouse Execution Software by filling the gaps between the TecSys WMS system and the material handling and order fulfillment technologies. This bridge was accomplished with a single point of interface and support and with a common database.
The result is an omni-channel, warehouse automation solution that meets the client’s growth expectations and dramatically reduces labor costs, while increasing order fulfillment accuracy.